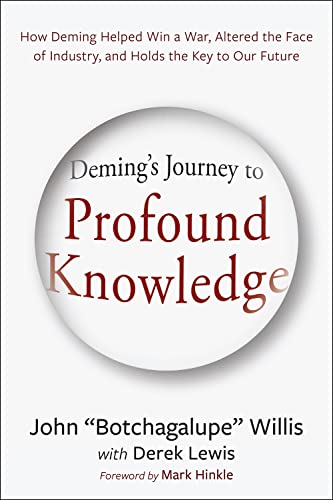
Deming’s journey to profound knowledge – How Deming helped win a war, altered the face of industry, and holds the key to our future by John “Botchagalupe” Willis may look like a biography of Deming, but it’s the story behind the story of his masterwork, which he shared with the world when he was ninety-three years old.
Just after he passed away in 1993, Deming’s book The New Economics was published. In it, he presented his masterwork, the culmination of his life’s experiences. He brought together all four pieces of Profound Knowledge and named it the System of Profound Knowledge (SoPK). It is encompassed by four elements and includes fourteen points of management and seven deadly diseases of management.
These four elements of Profound Knowledge are:
1. A Theory of Knowledge: How do we know what we believe we know?
2. A Theory of Variation: How do we analyze and understand what we know?
3. A Theory of Psychology: How do we account for human behavior?
4. An Appreciation of Systems/Systems Thinking: Are we seeing the bigger picture?
The book is divided in four parts. In the first part – Foundations of profound knowledge – we travel via the Hawthorne Works, the Peloponnesian War (bricks counting), the Celestial police to the Shewhart cycle: Figure out what you want, make it, inspect it, figure out what caused the defects, go fix it, and then go through the whole cycle again, using feedback from your mistakes to continuously improve production quality. This was tweaked by Deming into the Deming cycle: “plan, do, check, act” method, or simply the PDCA cycle. In his later years, however, Deming came to rename ‘check’ as ‘study’. It becomes clear that Shewhard, as his mentor, played a huge role for Deming when building his Profound Knowledge.
Shewhart understood that all processes have variation, but patterns of variation in a process can reveal insights into future defects. That’s why Statistical Process Control is so phenomenal: It allows you to statistically predict defects before they occur. According to Shewhart’s Statistical Process Control, managers shouldn’t waste their time trying to fix every single problem. Instead, they should identify which ones can be predicted and fix them. The story of accuracy and standardization is, in reality, a story of pragmatism. At any given time, a standard is a measurement that suffices and that everybody agrees upon.
In the second part is focusing on two examples. With his foundational ideas as firmly formed, Deming took the principles of Profound Knowledge he’d begun to glean and began to apply them to the real world, first at the US Census and then in manufacturing supplies for World War II. His experiences
with these formative concepts shaped Deming and his budding System of Profound Knowledge.
Deming applied Shewhart’s statistical process control methods at the Census Bureau. Statistical process control (later known as quality control) is based on the premise that no matter what the system is, its output will vary (the Theory of Variation). Up until now, statistical process control had been used solely for manufacturing. That’s what Shewhart created it for. Deming’s genius was in realizing that it could be used anywhere.
- Shewhart gave us a way to continually improve a process.
- Deming gave us a way to continually improve a system.
- Shewhart showed us how to optimize an existing process.
- Deming showed us how to rethink the process altogether.
- Shewhart used statistics to improve manufacturing.
- Deming used statistics to improve everything.
After the war was over, Deming had the opportunity to take his ideas abroad, finding a second home in the nation of Japan. His experiences there would not only crystalize the tenets of Profound Knowledge but would also influence him as much as he influenced those around him. Eventually, he would have the chance to bring his methods back to his homeland.
Toyota Way:
- Kaizen: continuous improvement
- Jidoka: the machine stops when there’s a problem.
- Andon cord: any worker can stop the assembly line when there’s a problem
- Go to gemba: the supervisor immediately goes to the source of the problem.
- Just-in-time and kanban: replacing push systems with pull, “made-to-order,” systems.
Back home Deming taught not only practical statistics but also core management principles. His approach to management is exemplified in his 14 Points for Management:
- Mission focussed
- Adapt or die
- Stop inspecting quality
- The fallacy of the lowest bidder
- Never stop improving
- Train for a systems thinking mindset
- Don’t manage – lead
- No fear
- No silos
- No slogans
- Quality, not quotas
- No barriers to pride
- A self-learning organization
- Transformation is for everyone
Ultimately, these fourteen points would culminate in the four elements of the System of Profound Knowledge.
Even after his death in 1993, Deming’s influence and impact continued to grow in some of the most bleeding-edge transformations of the twenty-first century. E.g., the Digital Cambrian Explosion (Amazon, Apple, Google, Uber, Airbnb, Netflix, agile, lean, MVP, DevOps, CALMS, …), Covid-19, cybersecurity and many more.
Conclusion. By walking chronologically through Deming’s life, we get a picture of many brilliant people and their ideas who influenced Deming’s thinking and vice versa, ultimately culminating in his System of Profound Knowledge. After reading this book you understand that Deming’s heritage is much more than only the PDCA circle.
To order: Amazon.com
Pingback: What Is A Digital Ad Agency
Pingback: Overview of my year 2023 book reviews | Henny Portman's Blog