Quality Assurance vs Quality Control
Quality assurance (QA) and quality control (QC) are two different concepts that are important in maintaining the quality of products delivered to customers. QA focuses on preventing mistakes and defects in the product while QC focuses on identifying and correcting errors in the product. QA is a proactive process that involves setting standards, creating procedures and processes, and ensuring that they are followed correctly. On the other hand, QC is reactive and involves testing the product to identify any deviations from the standards and then taking corrective measures to rectify them. It is important to understand the differences between QA and QC to ensure that the products are of high quality, meet customer expectations, and comply with industry standards.
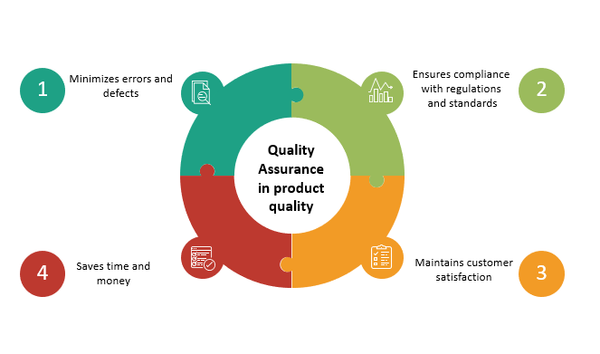
Understanding the Difference Between Quality Assurance and Quality Control
- Quality Assurance (QA) and Quality Control (QC) are two terms commonly used in the field of product and service delivery. While the two are related, they have different definitions and functions.
- Quality Assurance (QA) refers to the proactive measures taken in the design, development, and implementation of a product or service to ensure it meets the desired quality standards. It involves the creation and implementation of systems and processes designed to prevent defects, errors, and mistakes from occurring in the first place. QA is designed to ensure the continuous improvement of the product or service to meet ever-changing quality standards.
- On the other hand, Quality Control (QC) is the process of inspecting and testing a product or service to ensure that it meets the desired quality standards. It involves the identification and correction of defects, errors, and mistakes. QC is reactive, meaning it is done after the product or service has been developed or provided.
- While both QA and QC are important aspects of delivering high-quality products and services, they have different goals and approaches. QA is focused on preventing defects, while QC is focused on identifying and correcting them. Both QA and QC are necessary to achieve the desired level of product or service quality.
The Importance of Quality Assurance in Ensuring Product Quality
- Minimizes errors and defects: The primary aim of quality assurance is to identify and prevent errors and defects in the product development process. By doing so, it reduces the chances of faulty products being released to the market, which can be harmful to consumers and can damage a company's reputation.
- Saves time and money: Quality assurance helps to identify potential problems early in the development process, which reduces the likelihood of costly product recalls and delays. This, in turn, saves both time and money.
- Ensures compliance with regulations and standards: Quality assurance helps to ensure that products meet all necessary regulations and standards. Non-compliance can result in legal action, product recalls, and harm to consumers.
- Maintains customer satisfaction: A product that consistently meets consumer needs and expectations is crucial to maintaining customer satisfaction. Quality assurance helps to ensure that products are functional, reliable, safe, and meet the consumers’ needs, which increases customer loyalty and ultimately leads to increased sales.
The Role of Quality Control in Detecting Defects and Improving Product Quality
- Inspection: Quality Control uses different inspection techniques to catch defects in the production process. The inspection process includes visual inspection, measurement, and performance testing. Quality Control checks the raw materials, intermediate products, and finished goods to make sure the products meet the required standards.
- Testing: Quality Control runs several tests to determine the quality and durability of products. Different tests involve destructive and non-destructive testing, tensile testing, and load testing, among many others. These tests help to identify potential risks in products and ensure products meet customer satisfaction.
- Corrective Actions: If defects are detected, Quality Control takes corrective actions to fix the issues and prevent similar issues in the future. Actions may include adjusting the production process, improving training modules, or taking corrective actions to help mitigate potential risks.
The Benefits of Implementing Both Quality Assurance and Quality Control
- Improved product quality: By implementing Quality Assurance and Quality Control processes, a company can ensure that its products meet the highest quality standards possible, which can result in greater customer satisfaction and repeat business.
- Reduced costs: By catching defects early and continually improving processes, a company can reduce costs associated with fixing mistakes and reworking products.
- Better compliance with regulations and standards: Quality Assurance and Quality Control can help a company meet regulatory requirements and industry standards, preventing fines, legal issues, and damage to the company's reputation.
- Increased efficiency: Quality Assurance and Quality Control processes can identify inefficiencies in processes, allowing the company to streamline operations and increase productivity.
- Improved communication: By implementing Quality Assurance and Quality Control, a company can improve communication between different departments, resulting in better collaboration and faster problem-solving.
- Increased customer satisfaction: Customers expect high-quality products and services, and by implementing Quality Assurance and Quality Control processes, a company can exceed their expectations, leading to greater customer satisfaction and loyalty.
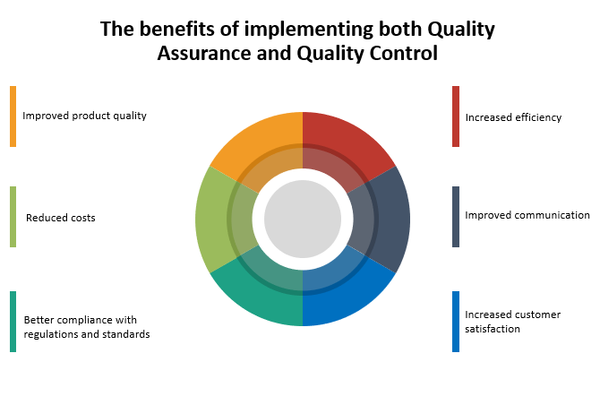
Tips for Implementing Effective Quality Assurance and Quality Control Practices
- Define clear quality objectives: Identify the specific goals, objectives, and expectations of the project or product, and ensure that the quality objectives are aligned with these goals.
- Establish a quality management system: Develop a set of policies, procedures, processes, and tools that enable the effective management of quality.
- Conduct regular quality audits: Conduct periodic quality audits to verify that the processes and procedures are being followed correctly, and to identify any areas that need improvement.
- Use testing and inspection techniques: Use appropriate testing and inspection techniques to identify any defects or problems in the product or process. This may include automated testing tools, manual testing, and visual inspections.
- Ensure that corrective actions are taken: If any defects or problems are identified, ensure that appropriate corrective actions are taken to address them and prevent them from recurring.
Conclusion
In conclusion, both quality assurance and quality control are crucial elements in the quality management process. Quality assurance is focused on preventing defects from occurring in the first place, while quality control is focused on identifying and correcting defects in products or services. By implementing a comprehensive quality management system that includes both quality assurance and quality control, organizations can improve their overall quality performance and enhance customer satisfaction. Choosing the right approach depends on the organization's goals and objectives. Therefore, businesses need to consider all the factors before deciding which technique will be suitable for their needs.