What Is SIPOC? Why Do We Need SIPOC?
In process improvement, a SIPOC is a tool that summarizes the inputs and outputs of one or more processes in table form. It is used to define a business process from beginning to end before work begins. The acronym SIPOC stands for suppliers, inputs, process, outputs, and customers, which form the table's columns.
What Is A SIPOC Model?
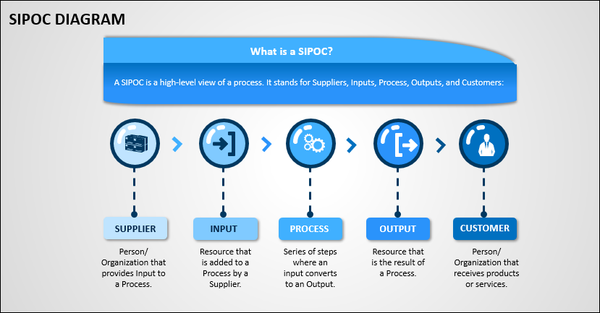
SIPOC stands for Suppliers, Inputs, Process, Outputs, and Customer, and these together form the columns of a SIPOC diagram. SIPOC model is a Six Sigma tool that organizations often leverage to document business processes from beginning to end. Since the diagram does NOT contain detailed information about processes, it is a high-level process map that gives an overview of a Six Sigma Project.
The core objective of using a SIPOC model is to ensure no shadow falls on your business projects. It makes your business operations more efficient.
First introduced in 1986 by Motorola Inc., the SIPOC is a part of the total equality movement. Later on, SIPOC got popularized as a part of the Six Sigma methodology, thereby becoming a core component of global business strategy. It aims to facilitate continuous improvement, better process management, and lean manufacturing.
Key Components Of The SIPOC Model:
The manufacturing industry employs the SIPOC model. Here, the suppliers and customers are the first and last components, external or internal to the business. Similarly, the inputs and outputs into the business process can be services, materials, or data.
Today, service industry companies generally follow the opposite of the SIPOC model viz. COPIES model where the customers are kept first. COPIES is an acronym for Customers, Outputs, Process, Inputs, and Suppliers. This is because in service sector companies such as food chains or restaurants, the customer puts up their demands first, and accordingly, they get the outputs. The output is facilitated through other components in the model, viz. Process, Inputs, and Suppliers.
Why Do We Need The SIPOC Model?
SIPOC is one of the most trusted and old-school methods used to map critical business processes in a high-level overview. It helps organizations graphically document their business processes, thereby visualizing key process elements via charts and tables.
Process management teams usually employ the SIPOC model in the “Measure” stage of the DMAIC (an acronym for Define, Measure, Analyze, Improve, and Control). DMAIC is one of the core tools that drive Six Sigma projects. The use of SIPOC in this stage helps identify peak factors of process improvements before actually starting to work on the project.
With the SIPOC model, teams consider various key process elements, such as suppliers, essential inputs into the process, various functionalities of the process, desired outputs from the process, and the end-user who will benefit from the outputs.
SIPOC is an intuitive visual tool that helps teams understand and overview the entire business process. With this model, you will get invaluable insights into various problematic areas where risks often arise. Major issues often arise from suppliers, specifications of input, or from the processes themselves, or poor outputs that are not capable enough to satisfy customers.
In the SIPOC diagram, the stakeholders, teams, and top management will identify and troubleshoot issues related to processes and make well-thought strategies for process improvements.
Representing the different elements of a process in a table or a chart helps keep everyone on the same page, even the new hires. In addition, all the involved teams will be informed about the different stages of a process.
By the same token, the SIPOC model also helps define variations in KPOV (Key Process Output Variable) - a factor that often derives as an outcome of a process. These variations have a considerable effect on performance, efficiencies, reliability, and manufacturability. Therefore, monitoring, identifying, and amending the variations will further drive process integration, process optimization, and improvements.
SIPOC Model Example
As stated, the key objective of a SIPOC diagram is to identify relevant elements in a business process. For this, the diagram quantifies inputs, the suppliers to provide the inputs, and the process that delivers the outputs. Therefore, to create the SIPOC diagram, teams must be able to map the entire operations involved.
Here’s an example of how a SIPOC diagram generally works. Let’s take an example of a car repair workshop. To form the SIPOC table, you need to create five columns with the name of five components that form the word “SIPOC.” They are as follows:
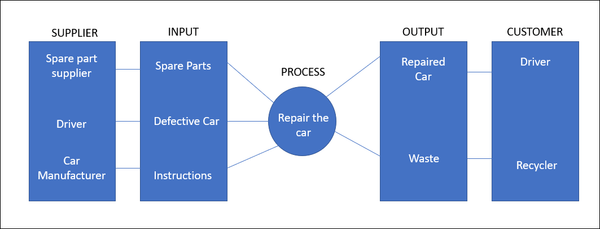
Example of SIPOC
- Supplier: Suppliers for the repair kit and spare parts, original part manufacturer, car owner, a customer representative.
- Inputs: Requisition for car repair, the car to be repaired, formal work order to proceed, and approved spare parts.
- Process: Diagnose the problem, source the required spare parts, use the right repair kit, carry out the repair, notification of car repair completion.
- Outputs: Repair recommendations/suggestions, cost evaluation, delivery schedule, repaired car, notification to the customer about completion.
- Customer: Car owner, a customer representative.
Once the SIPOC diagram forms, process management teams will share the model with related stakeholders for process improvements, evaluation, and future rectifications.
Secondly, let’s take a simple example of an ice cream stand:
- Supplier: Supplier for ingredients, customer demand.
- Inputs: Milk solids, water, sugar, flavors, preservatives, nuts, scooper, money drawer.
- Process: Prepare the ingredients, make the ice cream in a mixer, and cool it in the freezer.
- Outputs: Serving chilled ice cream in various forms (cones or cups), happy customer, order receipt, payment.
- Customer: Outlet customers, online customers, and even the ice-cream stand owner are customers when buying the ingredients.
This is a straightforward example of creating a SIPOC diagram to explain how detailed the model is supposed to be. Process management teams should include minute elements and operations involved and put them in the optimal column of the diagram.
Using SIPOC diagrams in your projects will definitely help the teams avoid the shadow.
How Does The SIPOC Model Help in Process Improvements?
The SIPOC model provides a clear overview of the entire process involved in the SixSigma Project and the follow-up steps. With the diagram, process management teams will be able to visualize the process, understand its key elements and interact with important entities such as stakeholders, top management effectively.
As teams get deeper insights into the main culprits causing the problems, enterprises will build practical strategies for rectifications and process improvements. The SIPOC model practically helps process management teams comprehend how Suppliers, Inputs, and processes affect the Outputs and Customer demands. Getting in-depth insights into the factors that impact the customers or end-user develops opportunities for significant improvements.