History of Six Sigma
Although Six Sigma was originally introduced in the 19th century with the bell curve by Carl Fredrick Grauss, it turned out to be inadequate and needed some corrections.
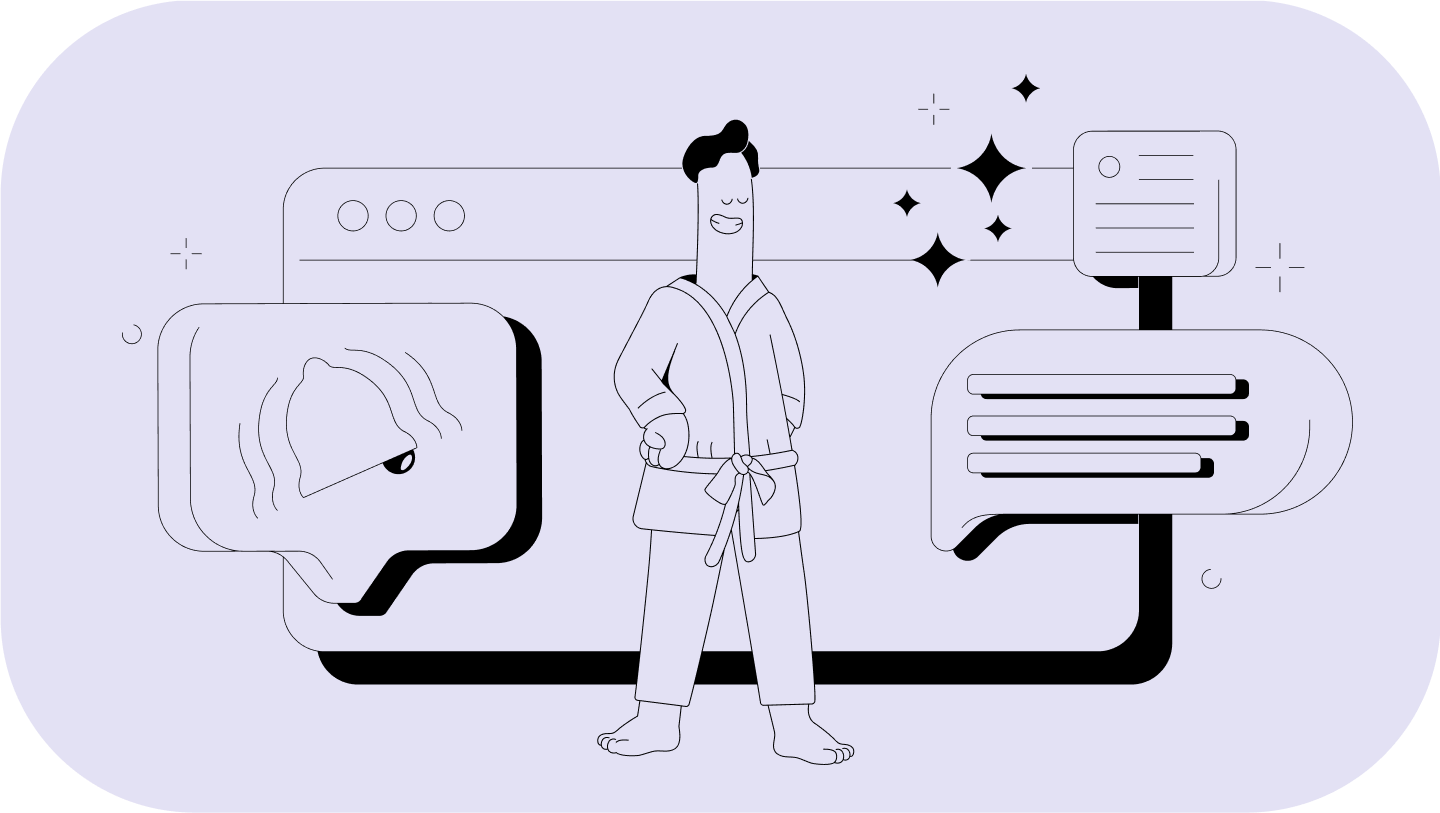
Six Sigma is a problem-solving methodology aimed at improving business and organizational performance by using several methods and tools. It primarily identifies and corrects errors and defects in manufacturing and business processes.
The six sigma methodology is mainly used in manufacturing processes to help companies reduce the number of defects. However, this method proved to be much more efficient in the short rather than the long run. By combining it with the lean principles, managers have been able to apply lean six sigma to other industry branches as well.
Although Six Sigma was originally introduced in the 19th century with the bell curve by Carl Fredrick Grauss, it turned out to be inadequate and needed some corrections.
It was brought back to life in the mid-1980s when Motorola faced a crisis: their product had poor quality, which affected their competitive advantage as they struggled to beat the competition and secure their place on the market. During the same decade, two other methodologies were also developed: PRINCE2 and the Theory of constraints.
Motorola came up with an idea to develop a Six Sigma Management System and reduce the variations in manufacturing processes that were causing defects. The results were stunning.
The quality of certain Motorola products experienced a tremendous increase, which encouraged other big corporations to follow the same path. Since then, many worldwide organizations have adopted the Six Sigma approach with all its tools and techniques and have saved hundreds of billions of dollars.
Engineers at Motorola developed a scale that should evaluate the quality of processes based on their defects. Six Sigma is at the top of the scale, which is 99.9997% defect-free. In other words, if you make a million car cylinders, there will only be 3.4 defects. This means that if your processes run at Six Sigma, they almost have no defects.
The Six Sigma scale shows how well an important feature performs compared to its requirements. The lower the sigma level, the bigger the number of defects. Naturally, most businesses operate at 4 or 5 Sigma, which means that the losses that result from poor quality cost them 10-15% of their revenue.
To improve the quality of the DMAIC model, there are various tools, all of which can be divided into two categories: process optimization tools that allow you and your team to create more efficient workflows and statistical analysis tools that let you analyze data more efficiently. To be able to do calculations, you need to incorporate the tools into Six Sigma software, which will do the rest of the job for you. Here are some of the essential tools that almost every Six Sigma Model uses.
It will help you identify customer requirements and rate them on a numerical scale. Next, you list various design options based on their ability to address customer needs. Finally, the designs with the highest scores will become the solution you should implement.
It helps you define which variables you should study further. First, you start with the specific problem and list all the variables in their respective categories affecting the problem. After listing all the variables, the expert team should determine which variables are most likely to be causing the problem. The diagram looks like a fish skeleton, hence the diagram's name.
It helps you identify, explore, and display all the possible causes and finally find the root cause of the problem. The cause-and-effect matrix is also called the X-Y diagram, Prioritization Matrix, and Correlation Matrix. Firstly, customer requirements are identified and prioritized. Next, key input variables are listed, and you look for a correlation with customer outputs. Once you rank each input and cross-multiply customer outputs, you’ll be able to identify the critical variables and improvement areas.
This tool allows you to focus on other processes and activities other than the issues that arise during the project development. This lets you list all possible failure scenarios, develop solutions, and rank them according to how well they address your concerns. Finally, your team can prioritize things that could go wrong and develop necessary preventive measures.
The Six Sigma methodology is defined by 5 DMAIC steps. DMAIC is a problem-solving technique that can help you handle any problems you meet along the way. It includes five main steps:
You need to define the problem and outlay your objectives. Your definition should include the exact problem with numeric representation and shouldn’t be vague.
Once you define your problem, you need to decide what measurements to use to quantify the problem. You have to identify what part of the product is damaged when they were damaged and the level of the damage.
After measuring, the next step is to collect and analyze data. At this point, it’s important to determine whether the error is valid or happened randomly, without any specific cause. You can use the collected data to compare it against measurements and evaluate its success.
The next stage includes developing solutions to the problems. Your team should create a test and launch pilot studies to find the most appropriate solution. After coming up with a solution, your team can start building a plan and developing a timeline.
Finally, to keep things under control and prevent a recurrence, you need to perform monthly, daily, or yearly control measurements.
While DMAIC focuses on the current processes, DMADV is focused on the process of designing a new product. Its phases include:
Defining— the goal and purpose of the project, product, or service. The main project manager's role is to take into special consideration the main stakeholders' requests
Measuring— CTQs or critical to quality factors. A thorough research of the market is necessary, and transforming customer requirements into defined goals
Analyzing— the best possible design option that will meet the goals and requirements
Designing— the chosen alternative, developing a high-level design, and testing the product or service
Verifying— whether the stakeholders accept the design. Making sure that the designed product works properly and meets all the quality standards
After the big Motorola success, many companies, from manufacturing and transactional industries (banks and hospitals) to the oil and entertainment industries, have incorporated the six sigma methodology and training in their framework.
For example, while General Electric profited from $7 to $10 billion in 5 years, Bank of America saved hundreds of millions within the first 33 years of launching Six Sigma.
Six Sigma is inevitably a path to dramatic improvement and brings immense value to organizations and customers.
Lean Six Sigma combines lean management and six sigma to improve performance by reducing waste and process variation. It appeared in the early 2000s as a synergy of the six sigma method originating in the 1980s and the lean methodology, which dates back to the 1940s.
The DMAIC phases are the basis of lean six sigma, but it's more focused on processes that tend to produce any kind of the eight types of waste: defects, overproduction, waiting, non-utilized talent, transportation, inventory, motion, and extra-processing. This list is usually summarized by the acronym DOWNTIME.
Unlike "regular" six sigma, lean six sigma is set on preventing the occurrence of defects rather than detecting and solving them. Several techniques are used to achieve this goal: Kanban, value stream mapping, kaizen, and the 5S tool.
Since most large corporations and big industries incorporate Six Sigma into their business strategy, the incorporation process requires ample time, training, energy, and huge financial resources.
At its core, we can incorporate Six Sigma in two standard ways:
• Through a separate organization that provides services to the main business
• By making it an integral part of every employee’s job
No matter what approach you choose in the project management life cycle, you need to keep in mind that Six Sigma focuses on the team and not on the individual. Each team has a certain level of certification that depends on the degree of their expertise and responsibilities. But what is a six sigma certification? It's a program that teaches individuals how to analyze and improve processes. You can learn how to implement the six sigma methodology or lean six sigma and go through several levels, from the white to the master black belt.
Teams and certifications are categorized as follows:
Black Belt— represents professionals and experts who need to have the training, a high degree of expertise, and a wide knowledge of all Six Sigma tools and methods. The current average annual salary is $123,078 in the US.
Green Belt— represents people who are in charge of solving a number of issues that arise in the manufacturing environment (if some issues become more complex, they can always consult the Black Belt). They usually handle professional administration and organization. According to Glassdoor, the average salary in the US for this role is $73,080 per year.
Yellow Belt— everyone else on the team. These employees don’t know every project detail and therefore don’t need extensive training and knowledge of Six Sigma. However, they are essential to success as they help Green Belts with the implementation of their goals.
The success of six sigma depends on the application of five principles.
The process begins with the customers and finding out what’s important to them and in what measure. Only when the company knows what quality means in terms of market standards and customer requirements can it improve the product’s quality.
The issue must be identified before it can be solved. So, you must assess the value chain and gather data. It’s important to know which data you need to be able to collect it correctly. Once you can view the right data, you can use it to identify the root cause of variation.
Once you’ve found the root of the problem, you must make changes to the process and eliminate any activity that doesn’t add value to the customer. You shouldn’t wait for problems to arise to go through these changes, but rather proactively survey customer satisfaction and overview the process to find opportunities for growth and potential improvement spots.
A six sigma team is usually composed of management, stakeholders, and team members trained in six sigma methods who excel in communicating with both clients and other team members. The variety of the team plays a crucial role in spotting variations and improving processes.
The changes we talked about must be implemented and accepted. If the team is rigid, it won’t be easy to make the necessary changes to the processes, which is the main focus of six sigma. One of the most important steps is to explain the benefits of the change to employees before proceeding with its implementation, so the team can be motivated to be part of the change rather than just execute it.
Get familiar with the most popular methodologies modern project managers use! Learn the basics and choose the best method to manage your teams and projects.
Choose the best methodology for your teams